Concrete Scaling: Causes, Sign, Prevention, Repair and Consideration
Concrete scaling involves the deterioration of the concrete’s surface layer, leading to flaking, peeling, and other forms of surface damage. This condition affects the appearance and durability of concrete surfaces, resulting from exposure to harsh environmental conditions or improper material application.
Concrete scaling is caused by repeated freeze-thaw cycles, which cause the concrete surface to expand and contract, and the use of de-icing chemicals, which erode the surface, according to a report by American Concrete Institute Committee et al. 1993, “Causes Evaluation and Repair of Cracks in Concrete Structures.” Poor curing practices, inadequate finishing techniques, and low-quality concrete mixes also contribute to the problem, weakening the surface and making it more susceptible to damage.
Signs of concrete scaling include surface flaking, peeling, and the formation of shallow depressions, according to Williams CE et al. 1944, “Concrete Scaling.” Additionally, exposed aggregate, rough or uneven textures, and discoloration indicate concrete scaling. Recognizing these signs early is crucial to prevent further deterioration.
Preventing concrete scaling involves using a high-quality concrete mix with proper air entrainment, applying a protective sealer, and ensuring adequate curing and finishing techniques. Regular maintenance, such as sealing and avoiding corrosive de-icing agents, also protects the concrete surface from scaling.
Considerations for repairing concrete scaling include removing damaged surface layers, applying suitable patching compounds, and ensuring proper curing of the new layer. Using a high-quality sealer after repair prevents future scaling and maintains the surface’s integrity. Each step addresses both the immediate and long-term needs of the concrete surface to ensure its durability and appearance.
What is Concrete Scaling?
Concrete scaling is a type of surface deterioration where the top layer of concrete peels, flakes, or chips away. This degradation occurs due to freeze-thaw cycles, where water enters the concrete, freezes, and expands, causing the surface to break apart. It also results from poor finishing techniques, insufficient curing, or the use of de-icing salts. Scaling is superficial and affects the appearance and durability of the concrete surface but only compromises its structural integrity if left untreated, according to a paper by the National Ready Mixed Concrete Association, 1998, “Scaling Concrete Surfaces.”
To maintain concrete surfaces, use a high-quality, well-cured mix with air entrainment to resist freeze-thaw cycles. Apply a sealer to protect against moisture and chemicals. Ensure proper surface preparation and finishing, and use non-corrosive de-icing agents to prevent scaling and extend the lifespan of the concrete.
What Causes Concrete Scaling?
Concrete scaling is caused by environmental and material factors, including exposure to freeze-thaw cycles, the application of de-icing chemicals, and poor curing and finishing practices, according to a report by American Concrete Institute Committee et al. 1993, “Causes Evaluation and Repair of Cracks in Concrete Structures.” Exposure to freeze-thaw cycles leads to the expansion and contraction of the concrete surface, which causes it to crack and deteriorate. The application of de-icing chemicals exacerbates the issue by eroding the surface and accelerating wear. Additionally, poor curing and finishing practices contribute to scaling by weakening the surface, making it less resistant to these environmental stresses. Together, these factors compromise the durability and appearance of concrete surfaces.
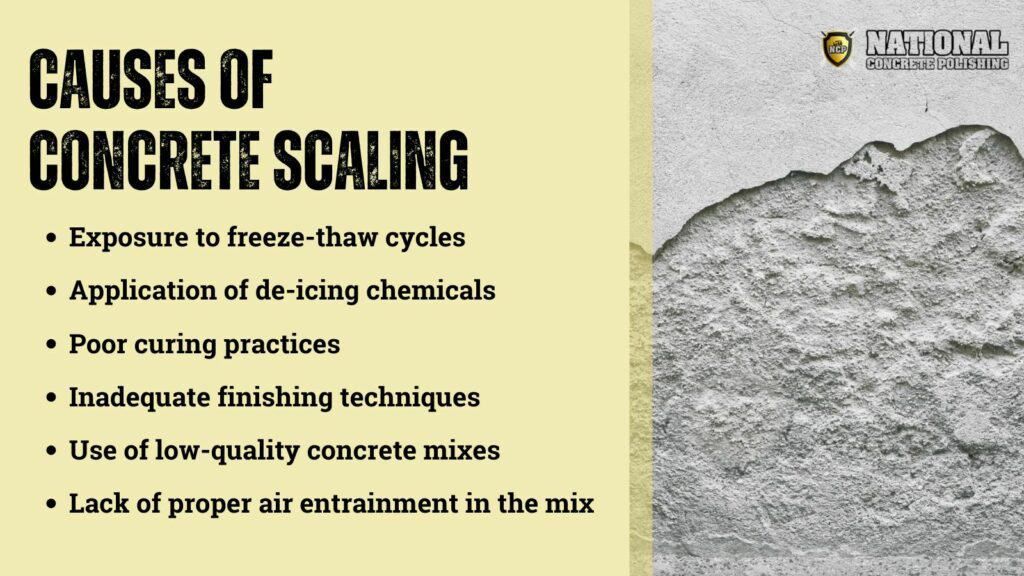
The top 6 causes of concrete scaling are as follows:
- Exposure to freeze-thaw cycles
- Application of de-icing chemicals
- Poor curing practices
- Inadequate finishing techniques
- Use of low-quality concrete mixes
- Lack of proper air entrainment in the mix
Exposure to Freeze-thaw Cycles
Exposure to freeze-thaw cycles refers to the repeated alternation between freezing and thawing temperatures that concrete surfaces endure, causing physical stress and damage. Freeze-thaw cycles cause the water within the concrete to freeze and expand, then thaw and contract. This repeated expansion and contraction create internal pressures that lead to surface cracking and scaling. The damage is significant, leading to the loss of surface layers and compromising structural integrity. To avoid this, use air-entrained concrete, which contains tiny air bubbles that accommodate the expansion of freezing water. Proper curing and sealing also help protect the surface from moisture infiltration.
Application of De-icing Chemicals
The application of de-icing chemicals involves using substances designed to melt ice on concrete surfaces, which leads to chemical erosion and scaling. De-icing chemicals, especially those containing chlorides, penetrate the concrete surface and react with the cement paste, causing deterioration and scaling, according to a study by Misák P et al. 2023, “Effect of De-Icing Chemicals on Concrete Scaling: The Role of Storage Water.” This chemical erosion weakens the concrete and accelerates surface degradation. To mitigate scaling, non-corrosive de-icing alternatives are used, or their use is limited. Additionally, applying a high-quality sealer helps protect the surface from chemical penetration.
Poor Curing Practices
Poor curing practices refer to inadequate methods of maintaining optimal moisture, temperature, and time conditions necessary for the concrete to achieve its desired strength and durability. Insufficient curing leads to incomplete hydration of the cement particles, resulting in a weak and porous surface prone to scaling. This compromises the concrete’s resistance to environmental stresses. To prevent poor curing, ensure continuous moisture maintenance, use curing compounds, and follow proper curing durations based on environmental conditions.
Inadequate Finishing Techniques
Inadequate finishing techniques involve improper methods used to smooth and prepare the concrete surface, which leads to weaknesses and vulnerabilities. Poor finishing results in a surface that is too smooth or too rough, impacting the concrete’s ability to resist scaling. If the surface is not adequately completed, it does not bond well with subsequent layers or is more susceptible to environmental damage. To avoid this, employ proper finishing techniques, including appropriate troweling and texturing, and ensure the surface is neither too wet nor too dry during finishing.
Use of Low-quality Concrete Mixes
The use of low-quality concrete mixes involves employing materials with inadequate properties, such as insufficient strength, durability, or resistance to environmental factors. Low-quality concrete mixes need more strength and durability to withstand environmental stresses, leading to scaling and surface degradation. Such mixes need an adequate cement content or proper aggregate sizes. To prevent this, use high-quality materials and adhere to recommended mix designs, ensuring the concrete meets industry standards for strength and durability.
Lack of Adequate Air-entrainment in the Mix
Lack of adequate air entrainment in the mix refers to the insufficient incorporation of air bubbles within the concrete, which helps it withstand freeze-thaw cycles. Air entrainment creates microscopic air bubbles within the concrete, which provide space for water to expand when frozen, reducing internal pressure and preventing scaling. Without adequate air entrainment, the concrete is more susceptible to damage from freeze-thaw cycles. To avoid this issue, ensure that the concrete mix includes an appropriate amount of air-entraining agents, as specified by industry standards, to enhance its resistance to environmental stress.
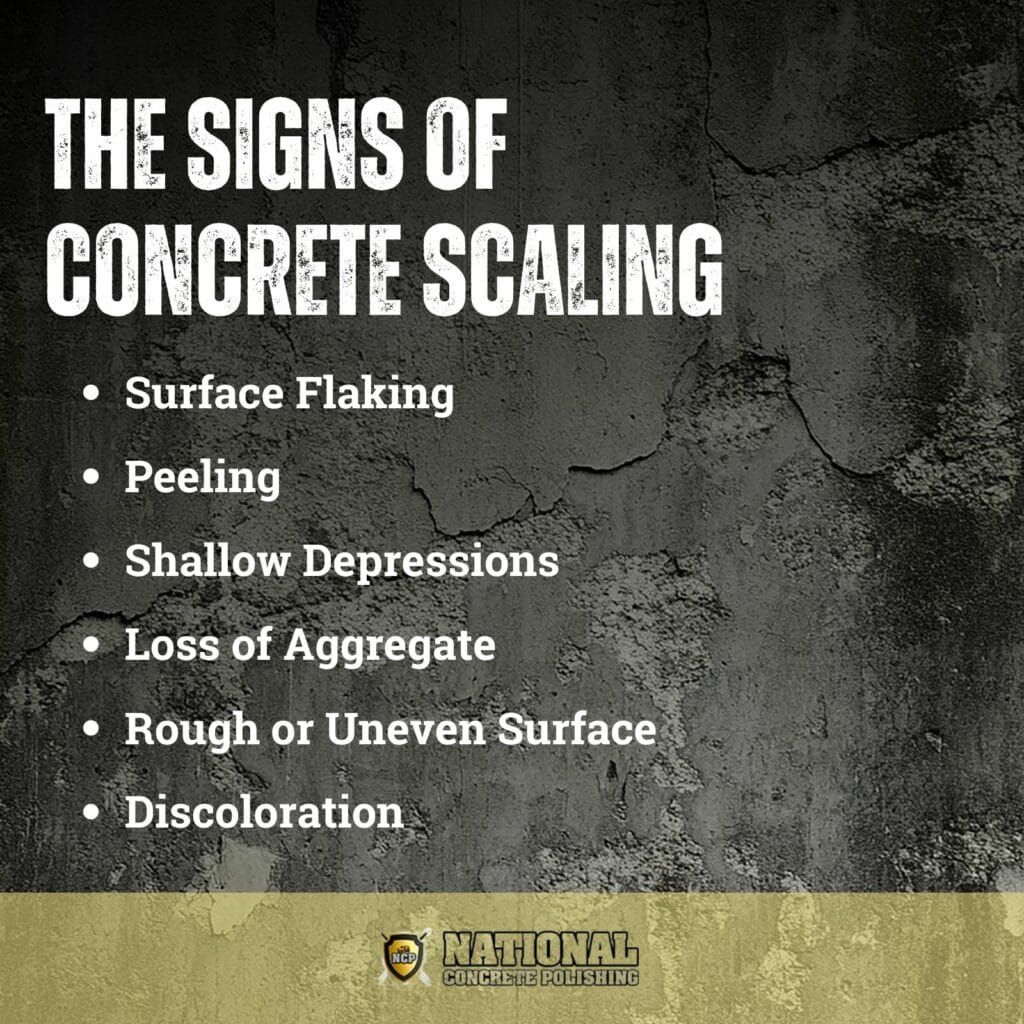
What are the Signs of Concrete Scaling?
Signs of concrete scaling include surface flaking, peeling, and shallow depressions where the top layer has deteriorated. Exposed aggregate, rough or uneven surfaces, and discoloration also indicate scaling, showing the concrete is breaking down, affecting both its strength and appearance, according to Williams CE et al. 1944, “Concrete Scaling.” Early identification allows for corrective measures to prevent further damage.
The signs of concrete scaling are as follows:
- Surface Flaking : Surface flaking refers to the detachment of small layers from the concrete surface. This sign indicates that the top layer is breaking down due to environmental stress or material failure. It is a serious issue as it exposes the underlying concrete and accelerates deterioration. Flaking appears early and is more common in outdoor applications subjected to freeze-thaw cycles and de-icing chemicals.
- Peeling : Peeling describes the removal of thin, detached sections from the concrete surface, revealing underlying layers. This indicates poor surface bonding or inadequate curing. It is a critical sign of scaling that leads to further surface damage and degradation. Peeling occurs soon after application and is prevalent in poorly cured exterior concrete surfaces.
- Shallow Depressions : Shallow depressions are small, dimple-like indentations on the concrete surface. They show where the surface layer has worn away due to scaling. These depressions are significant as they compromise the surface’s integrity and lead to further deterioration. They appear relatively early and are especially noticeable in high-traffic areas and surfaces exposed to harsh weather.
- Loss of Aggregate : Loss of aggregate involves the exposure of stones or gravel that were previously embedded in the concrete surface. This sign indicates that the surface layer has eroded, exposing the aggregate beneath. It affects the concrete’s strength and durability. This sign is apparent early in the scaling process and is common in surfaces exposed to extreme weather conditions and de-icing chemicals.
- Rough or Uneven Surface : A rough or uneven surface refers to a textured, irregular appearance due to the degradation of the concrete. This indicates significant scaling and erosion, affecting both functionality and aesthetics. The concrete appears to continue deteriorating, and it is seen in heavily trafficked areas and surfaces subject to freeze-thaw cycles.
- Discoloration : Discoloration involves changes in the concrete’s color, appearing as patches or uneven tones. This signals surface damage and scaling. It is a less severe but visible sign that indicates underlying issues with the concrete’s surface. Discoloration appears relatively early and is observed in areas with inconsistent exposure to moisture and environmental stress.
How to Prevent Concrete Scaling?
To prevent concrete scaling, using a high-quality concrete mix with proper air entrainment to resist freeze-thaw cycles is required, according to a study by Jana D et al. 2007, “CONCRETE SCALING – A CRITICAL REVIEW.” Applying a sealer protects the surface from moisture and de-icing chemicals. Proper curing ensures adequate humidity and temperature conditions. to prevent scaling. Using the correct finishing techniques enhances surface durability and applies high-quality materials. Utilizing non-corrosive de-icing agents reduces chemical damage and prevents concrete scaling.
To prevent concrete scaling, follows steps need to be taken:
- Use a high-quality concrete mix with proper air entrainment.
- Apply a sealer to protect against moisture and de-icing chemicals.
- Ensure appropriate curing with adequate moisture and temperature conditions.
- Use correct finishing techniques to enhance surface durability.
- Select high-quality materials for construction.
- Utilize non-corrosive de-icing agents to minimize chemical damage.
What are the Key Considerations in Repairing Concrete Scaling?
The key considerations in repairing concrete scaling include first removing the damaged surface layers by cleaning and preparing the area to ensure proper adhesion. Next, apply a concrete patching compound or resurfacer specifically designed for scaling repair, adhering to the manufacturer’s instructions for mixing and application. Proper curing of the new layer is essential for achieving optimal strength and durability. Finally, applying a high-quality sealer helps protect the repaired surface from future damage and extends the repair’s longevity.
To repair concrete scaling, the following 4-step process is needed, according to a report by American Concrete Institute Committee et al. 1993, “Causes Evaluation and Repair of Cracks in Concrete Structures”:
- Step 1—Remove Damaged Surface Layers : This step involves cleaning and scraping away the deteriorated concrete to reach a stable base. Removing the damaged layer ensures proper adhesion of repair materials and prevents further scaling. Effective removal helps the new surface bond well and extends the repair’s longevity.
- Step 2—Apply Concrete Patching Compound or Resurfacer: This step involves using a specialized mix designed for repairing scaled surfaces. The compound or resurfacer is applied to the prepared area to restore a smooth, durable finish. The resurfacer fills in voids and covers the damaged areas, providing a renewed surface that resists further scaling. Proper application and curing enhance the repair’s effectiveness and longevity.
- Step 3—Ensure Proper Curing : This step involves maintaining adequate moisture and temperature conditions for the repaired surface. Proper curing helps the patching material achieve its full strength and durability. Effective curing prevents future scaling and ensures the repair remains intact over time.
- Step 4—Apply a High-Quality Sealer : This step involves coating the repaired surface with a sealer that protects against moisture and de-icing chemicals. The sealer acts as a barrier to prevent future scaling by shielding the concrete from environmental stressors. Regular reapplication of the sealer helps maintain protection and prolong the effectiveness of the repair.
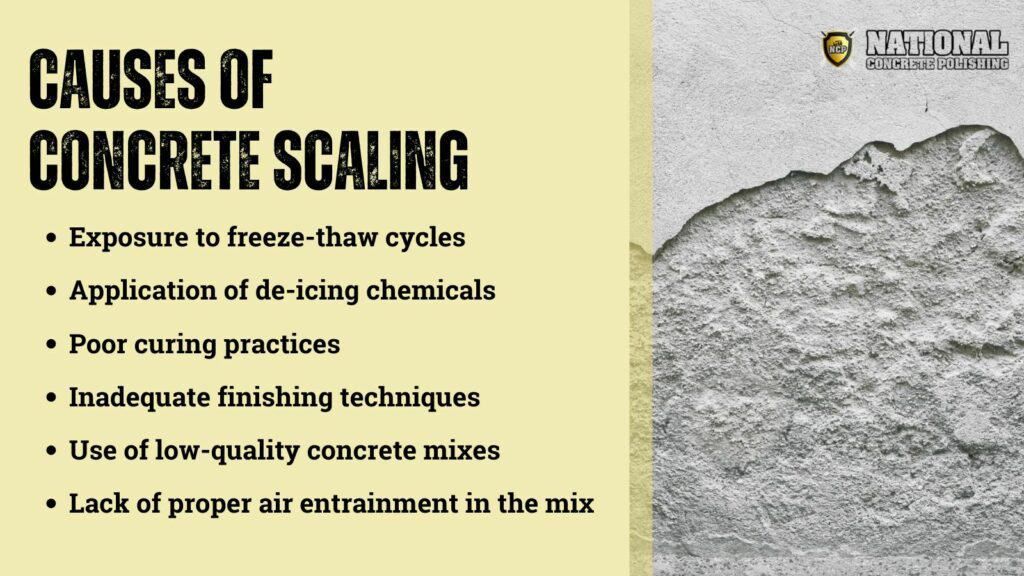
What is the Difference Between Concrete Scaling and Spalling??
The main difference between concrete scaling and spalling is that scaling affects only the surface layer, causing it to flake or peel, while spalling originates from deeper within the concrete, leading to the disintegration of larger surface fragments. Scaling is caused by freeze-thaw cycles and de-icing chemicals, which deteriorate the top layer. In contrast, spalling results from issues such as rebar corrosion due to carbonation, intense heat causing violent water vapor expansion, improperly constructed joints, or deteriorated cracks. These deeper issues in spalling lead to more severe structural damage and larger fragments compared to the surface-level deterioration seen in scaling.
To prevent and manage concrete scaling, focus on using high-quality concrete mixes with proper air-entrainment, applying sealers to protect against moisture and de-icing chemicals, and ensuring correct curing and finishing techniques. In contrast, preventing and repairing concrete spalling requires addressing deeper structural issues, including reinforcing or replacing corroded rebar, repairing cracks and joints properly, and using materials that withstand intense heat or moisture. Effective management of spalling involves more extensive repairs and possibly structural reinforcements to address the root causes of the damage.
What maintenance practices can help avoid concrete scaling in winter?
The maintenance practices that help avoid concrete scaling in winter include applying a high-quality sealer to protect the concrete surface from moisture and de-icing chemicals, according to a report by Peterman K et al. 2023, “Construction and Materials Best Practices for Concrete Sidewalks: Phase II – Long-Term Performance and Hot-Weather Placement Effects.” Additionally, using non-corrosive de-icing agents instead of traditional salts prevents surface damage. Ensuring proper curing before winter sets in helps the concrete achieve optimal strength. Regularly removing snow and ice from the surface to prevent prolonged exposure to moisture is also important. Finally, avoiding the use of metal shovels that damage the surface further contributes to preventing scaling.
What are the long-term effects of concrete scaling on structural integrity?
The long-term effects of concrete scaling on structural integrity include reduced load-bearing capacity, increased susceptibility to further damage, and diminished aesthetic appeal, according to a study by Luo S, Bai T et al. 2022, “Impact of Freeze-Thaw Cycles on the Long-Term Performance of Concrete Pavement and Related Improvement Measures: A Review.” Scaling causes the surface layer of concrete to deteriorate, which compromises its strength and ability to support weight. This deterioration leads to further cracks and damage as the underlying concrete becomes exposed to environmental stresses. Over time, the visual appeal of the concrete is also affected, which impacts the overall appearance of the structure. Addressing scaling promptly and implementing preventive measures are crucial to maintaining the concrete’s structural integrity and appearance.
How can I tell if my concrete is prone to scaling?
You can tell your concrete is prone to scaling by observing surface conditions such as early signs of flaking or peeling, checking for rough or uneven textures, and noting any discoloration or patchy areas, according to a paper by the National Ready Mixed Concrete Association, 1998, “Scaling Concrete Surfaces.” Flaking and peeling indicate that the surface layer is deteriorating, which is a clear sign of potential scaling. Rough or uneven textures result from the weakening of the surface due to scaling. Discoloration or patchy areas signal underlying damage and a higher risk of scaling. Additionally, environmental factors like exposure to freeze-thaw cycles and de-icing chemicals, which increase the likelihood of scaling, are considered. Regular inspections and addressing these signs early help prevent further damage.
You might also like
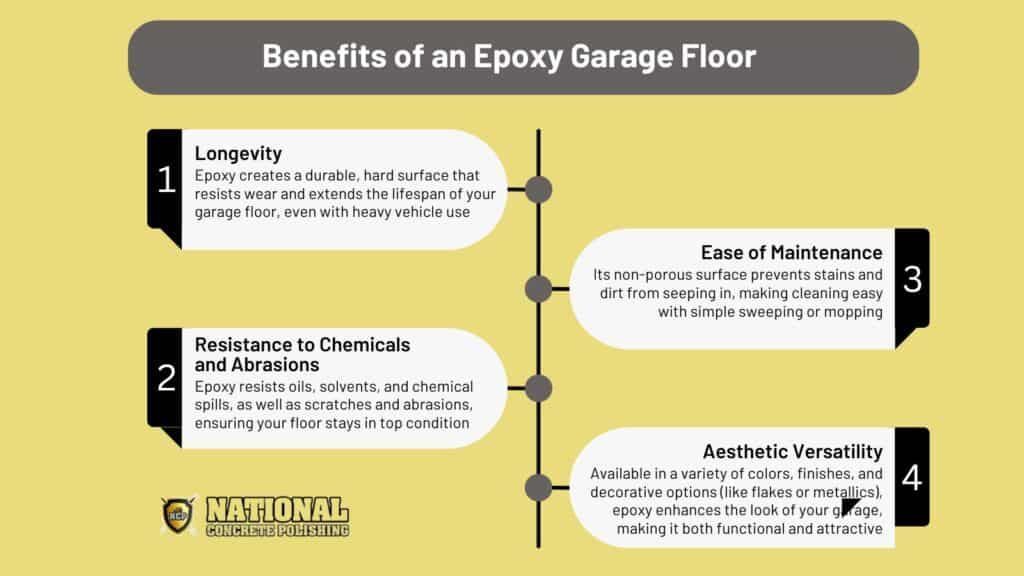
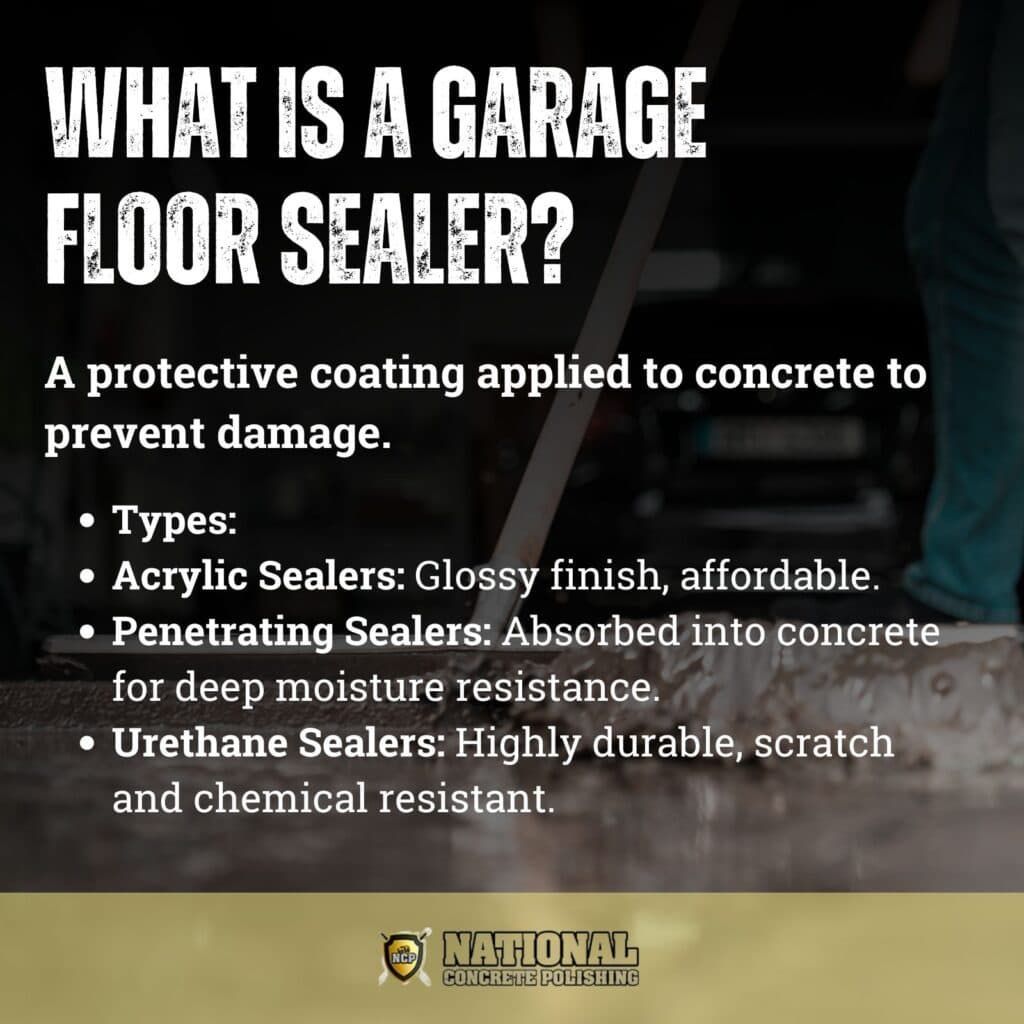
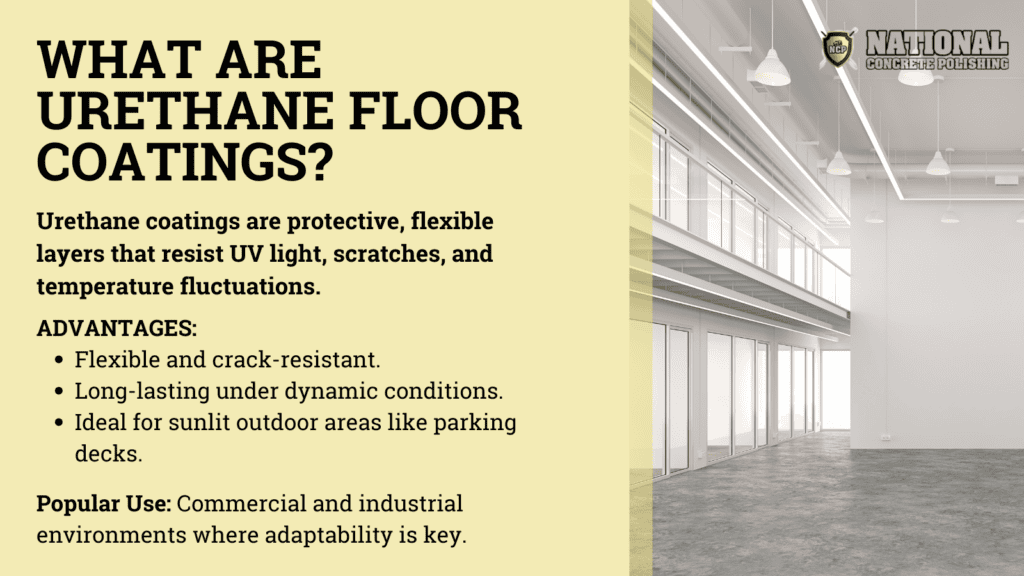